Expanded pellet feed came into being after the aquaculture industry developed to a certain stage. Expanded pellet feed should not only have balanced nutrition and good water stability, but also not affect the quality of the water environment where aquatic animals live, so it has achieved good results in the market. Word of mouth, for manufacturers who want to produce this feed, the aquatic feed production process flow chart is the blueprint to realize this wish.
Make Aquatic Feed Pellets for Commercial Purpose
ABC Machinery is one of the largest sellers and suppliers of pellet machines in China. His subsidiary Gemco has become a manufacturer integrating R&D, production, sales and after-sales. If you are interested in the performance of the equipment and how to establish a pellet machine factory, please contact us! Here can provide you with a complete service.
Typical Aquatic Expanded Pellet Feed Processing Flow Chart
Aquatic Feed Extruding Process for Fish Catfish Shrimp
Due to the wide variety of aquatic feeds, the large changes in raw materials, the high requirements for crushing fineness and the poor fluidity of the materials, the production process requirements for aquatic expanded pellet feeds are relatively high. The typical process flow mainly includes: receiving, cleaning, and coarse crushing of raw materials. Ingredients and mixing, secondary crushing, secondary mixing, conditioning and puffing, granulation and spraying, product grading and packaging and other processes,
1. Receiving, cleaning and coarse crushing of raw materials: aquatic feed pre-processing
The raw materials used in aquatic pellet feed production plants are mainly in the form of powder and pellets. Powder feed production does not require coarse crushing. This kind of raw material can be directly passed through the feeding pit and elevator, and then enter the conical cleaning screen to remove impurities. Then it is magnetically separated and directly enters the batching bin through the distributor or spiral auger. One batch of ingredients;
The production of pellet feed requires coarse crushing. The material enters the cleaning equipment through the feeding pit and elevator for magnetic separation and impurity removal, and then enters the bin to be crushed. After coarse grinding, it enters the batching bin through the elevator and distributor. Ingredients at a time. Primary coarse grinding is the pre-treatment process of ultra-fine grinding in aquatic feed processing. The main purpose is to reduce the particle size difference and variation range of materials, improve the working conditions of the ultra-fine grinder, improve the working efficiency of the ultra-fine grinder, and ensure stable product quality. .
2. One-time batching and mixing: add according to formula
The primary ingredients are mainly the preparation of common raw materials, that is, the preparation of materials with a large proportion in the formula, such as corn, rice bran, soybean meal, etc. This process is mainly completed by electronic batching scales. During the batching process, special attention must be paid to the arching problem of the batching bin. After the batching is completed, primary mixing begins. Primary batching and mixing are the pre-processing steps of ultra-fine grinding, which can reduce the variation range of material particle size, improve the working conditions of the crusher, increase crushing efficiency, and ensure product quality.
3. Secondary crushing: precise screening
Because aquatic animals have low food intake, short digestive tracts, and poor digestion capabilities, aquatic feeds are required to be crushed into very fine particles. For example, all shrimp feed must pass through a 40-mesh grading sieve, and less than 5% of the 60-mesh sieve must be screened. Therefore, it must be used Secondary crushing process. In the secondary crushing process, the primary mixed materials enter the bin to be crushed after being lifted, and then enter the secondary crusher. After the secondary crushing process is completed, they enter the rotating classification screen to remove the crude fibers in the feed formed during the crushing process. of tiny fuzz.
4. Secondary mixing: adding trace additives
Each raw material enters the secondary mixer after secondary batching. There is a manual feeding port above the secondary mixer for adding trace additives. There are two liquid adding devices on the mixer for adding grease and water respectively. During the secondary mixing process, each material must be thoroughly mixed, and the coefficient of variation CV is less than 5%. After being finely pulverized and mixed with secondary ingredients, the material enters the subsequent process - the puffing and granulating process.
5. Conditioning and extruding: correcting the moisture of the raw materials to generate pellets
In the extrusion and puffing process, the material is cooked for a period of time under high temperature, high humidity, and high pressure. During this process, the physical and chemical properties of the material undergo drastic changes (mainly starch gelatinization and protein denaturation). Instantaneous pressure drop, the moisture in the feed is converted from liquid to gaseous state, and is emitted from the feed, causing the material to expand, forming so-called expanded feed.
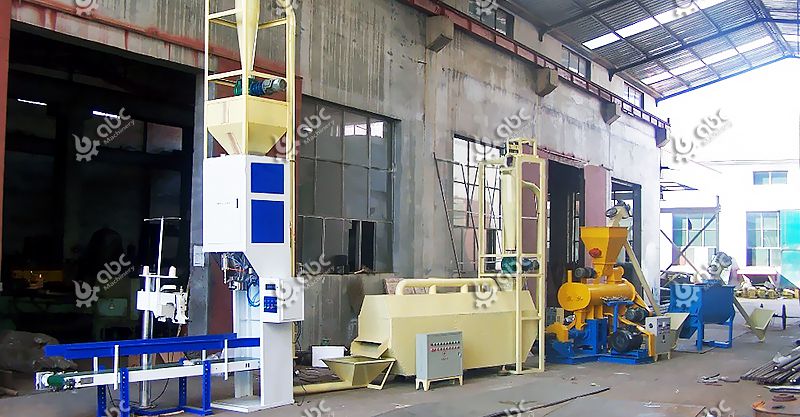
Aquatic Animal Food Manufacturing Equipment
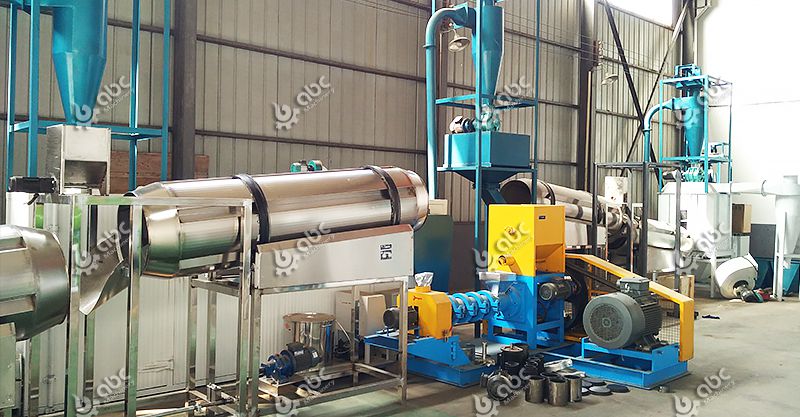
Aqua Food Processing Plants for Sale
6. Grease spraying on the surface of pellet feed
After the material is extruded by the extruder, it forms wet and soft particles (moisture content is 25% to 30%). In order to reduce the breakage of the particles, it is advisable to use pneumatic transportation and enter the dryer for drying, so that the moisture content of the material is reduced to about 13%. . After the material is dried, it enters the external spraying system, and the surface of the pellet feed is coated with oil, vitamins, flavoring agents, etc., which not only meets the energy needs of fish, but also reduces the loss of heat-sensitive substances during processing. It can also improve the palatability of feed and reduce the powder content. After the material passes through the external spraying system, it needs to be cooled and crushed.
7. Product grading and packaging
The cooled materials are lifted and crushed and then enter the grading screen for classification. The classification screen generally consists of two layers of sieves. The upper sieve needs to be returned to the crusher for crushing; the lower sieve is generally fine powder, which can be returned to the expansion bin for re-forming; the lower sieve has The finished products go directly into the finished product warehouse and are then weighed and packaged.
The above production process is the conventional configuration of the current aquatic expanded feed processing technology, which can produce sinking feed, slow sinking feed and floating feed. Although the extruded pellet feed processing technology has been recognized by many manufacturers as a new processing technology, it requires a large investment compared to the hard pellet feed processing technology, so it has not been widely used.
Why Choose Extruded Feed for Making Aquatic Feed Pellets?
Extruding Feed for Aquatic Animals
-
Good palatability: Extruded feed is appealing to animals, encouraging them to consume it willingly.
-
Avoids automatic grading of products: The extrusion process ensures uniformity in the feed, preventing segregation or separation of ingredients.
-
Easy to transport: Extruded feed has a stable form, making it convenient to transport without the risk of breakage or spoilage.
-
High degree of gelatinization of starch: The starch in extruded feed is effectively cooked, enhancing its digestibility and nutrient absorption.
-
Reduces waste during the feeding process: The digestibility of extruded feed reduces the amount of undigested material in animal waste, minimizing environmental impact.
If you want to buy a high-quality and affordable feed pellet machine, ABC Machinery is your best choice. Please fill in the details of your needs in the form below, and we will have professional business personnel to help you out!